What can 3D concrete printing be used for?
What CAN 3D Concrete Printing be used for?
3D Concrete printing has uses in onsite and offsite construction. Typically, it excels in onsite construction while using the principles of offsite construction. Some uses for 3D Concrete Printing are onsite: full builds from foundation to structure, industrial applications (e.g. wind turbine bases) offsite: functional facades, non-structural aesthetic elements, infrastructure elements and prefabricated building elements. While the technology does manage to provide some useful functionality in offsite construction, its primary purpose is onsite builds.
3D Concrete Printing (3DCP) is becoming a real option for companies in Ireland. To learn more about what 3D Concrete Printing is, you can read our blog post here.
Offsite Applications
One use case of 3D Concrete Printing is in offsite manufacturing, in a controlled manufacturing facility where it can be used to make prefabricated or modular elements that can be shipped to a construction site for assembly. This process is similar to how typical modular structures and precast builds are created and built, although there are some key areas where 3DCP really shines.
Façades
Individual elements with real functional uses can be printed for installation in a build. This can include bespoke joinery for one off projects, or multipurpose elements that can direct sunlight or air flow. The printer is extremely flexible in this and can be used to meet needs as they arrived. This introduces an element of agility to the build as you can make bespoke elements with relatively little investment of time and resources.
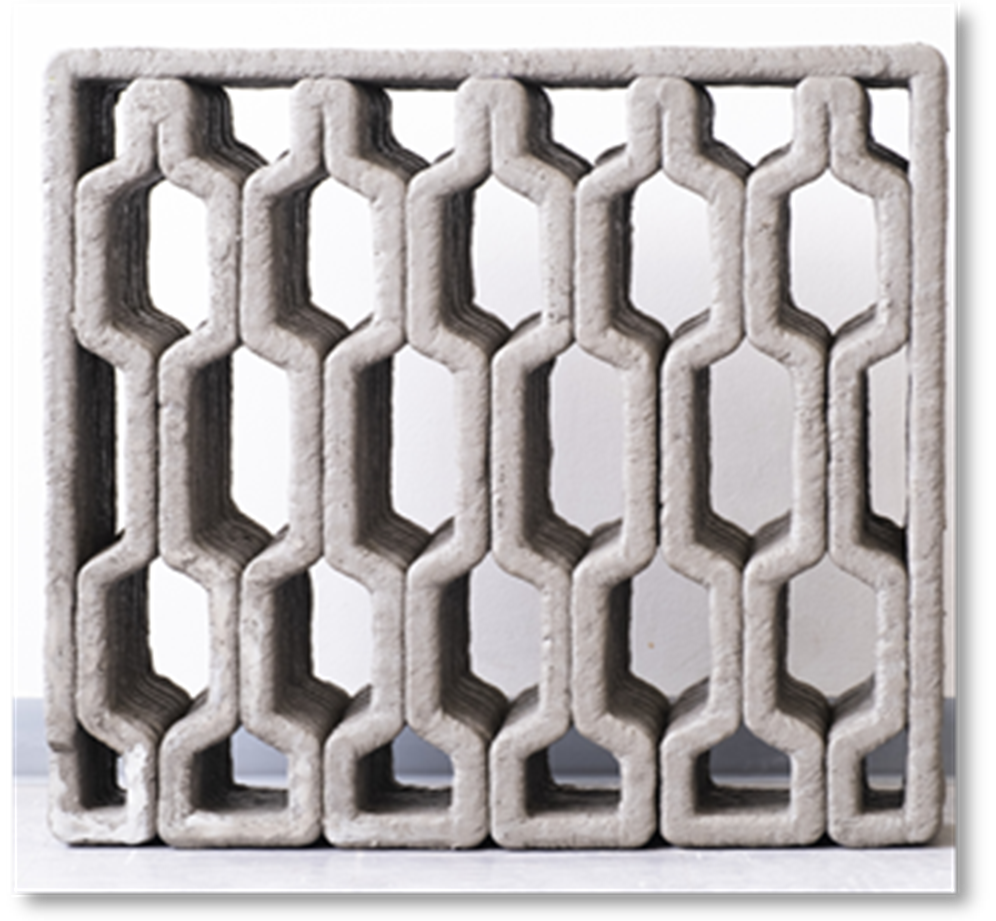
Advantages of 3D Concrete Printing for Facades:
- Can build individual elements
- High resolution to the millimetre
- High flexibility
- Can be used for bespoke joinery
- Multifunctional purpose (e.g. Directing sunlight)
Non-structural Aesthetic Elements
3D Concrete Printing creates opportunities for architects and designers to create innovative aesthetically pleasing sections to a build in a far more cost effective way than was previously possible. 3DCP technology allows for the development of quick, easy and inexpensive designs that can be used in a build to improve the aesthetic value. There is zero waste and requires very little design knowledge to create elegant structures.
Advantages of 3D Concrete Printing for Non-Structural Elements
- Flexible agile designs
- Adds aesthetic value
- Flow of forces – no excess materials f
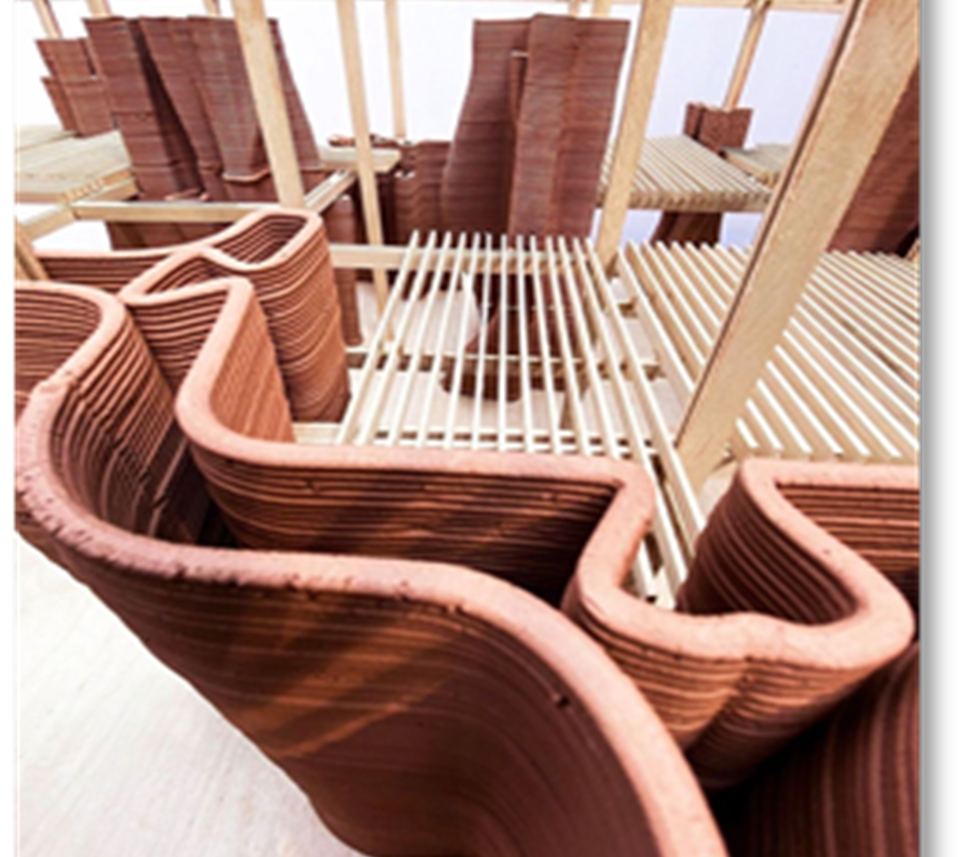
Infrastructure Elements
The primary advantage of the 3DCP in Infrastructure is that it can build incredibly strong structures with virtually zero waste. These builds can incorporate unique design elements, as seen in the image, with high tensile strength. These builds can be completely unique, slightly altered or produced in short runs depending on your needs with no extra costs.
Advantages of 3D Concrete Printing for Infrastructure
- Zero waste
- High resolution to the millimetre
- High flexibility
- Can build unique elements
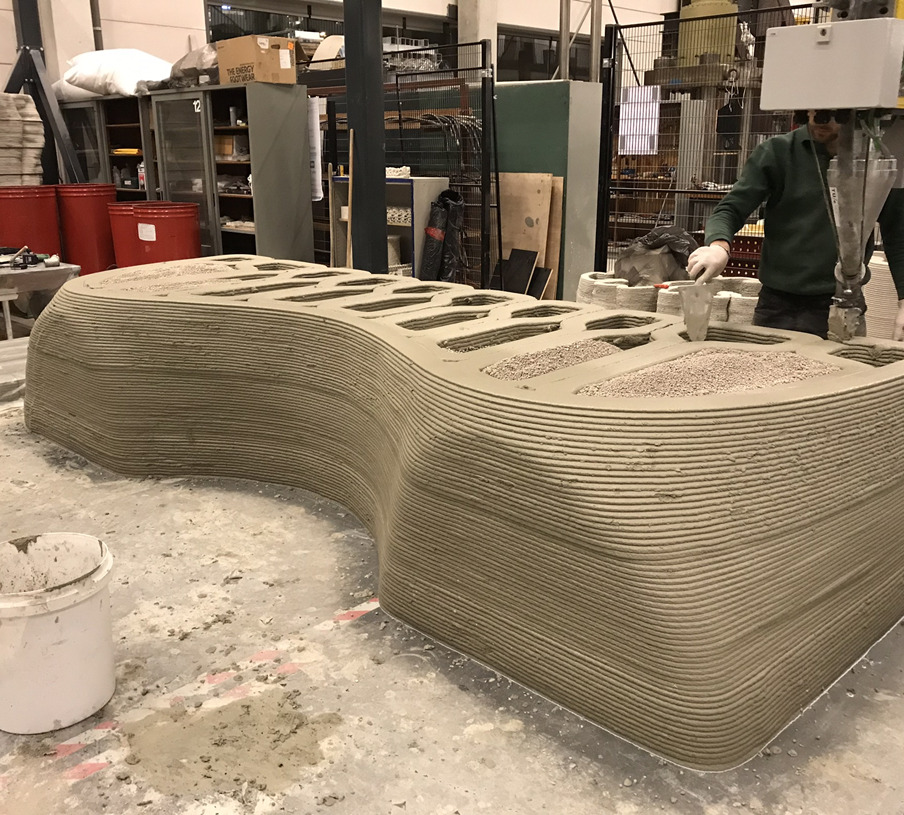
Prefabricated Building Elements
Another possibility for offsite building is to create building elements such as prefabricated wall panels that can be transported to and assembled onsite. This method is not particularly cost effective or useful, however it can beat out traditional methods or modular methods if a unique change needs to be made to a design.
Advantages of 3D Concrete Printing for Prefabricated Building Elements
- Highly Flexible
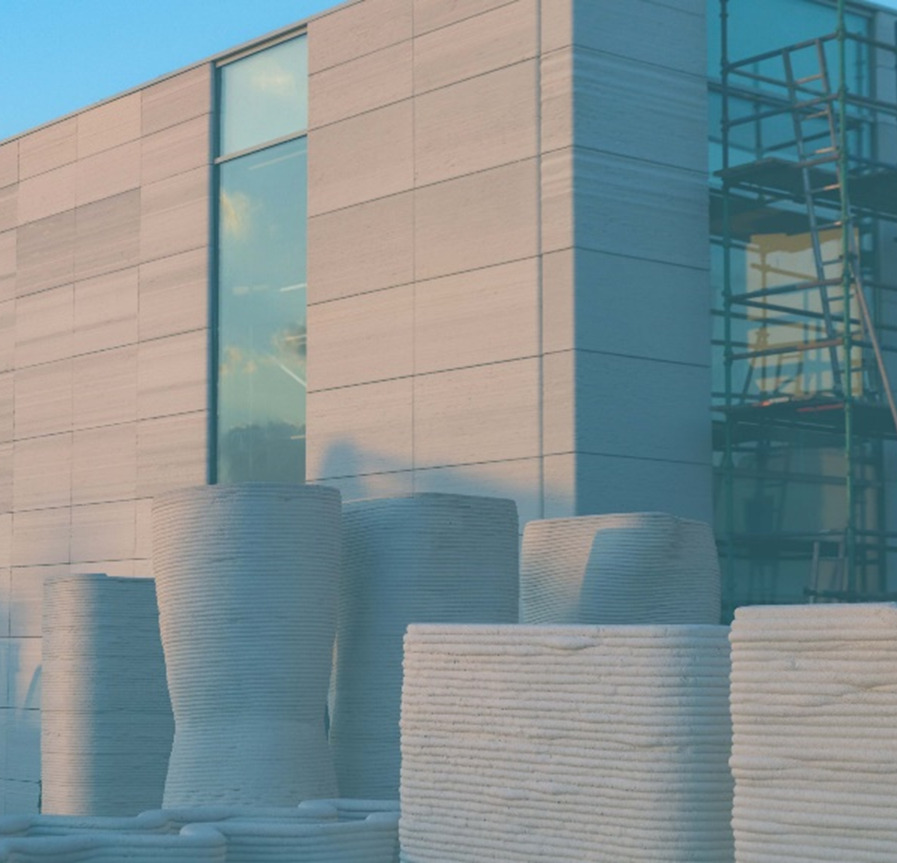
Onsite
Where we begin to see 3DCP really outdo traditional and offsite manufacturing processes is when we bring the machine onsite with us. Think of it as bringing the machinery and techniques of “offsite manufacturing” to the site. The machine can be quickly set up on a site with a poured foundation and begin a pre-determined print.
This technology is already being used across the world. In Germany 3DCP champions PERI have built residential apartment blocks with 5 units, as well as a series of residential 3 bed, 2 bathroom homes. In Belgium 3DCP has been used to build freeform proof pf concept buildings to showcase this the possibilities of this technology.
There are many advantages to this approach to building, most notably the freedom to innovate without any additional cost. Making changes or adding complexity to a drawing will add minimal to no extra cost into the build. Architects have far more freedom to design aesthetic and functional buildings without the hefty price tag.
Industrial Applications
Another area in which 3DCP is breaking ground is in industrial infrastructure. A major difficulty in modular construction has been transporting precast wind turbine bases to a remote location where they have to be erected. 3DCP provides an elegant solution where the machine can be brought onsite and used to quickly and easily erect a strong wind turbine base, higher than its modular counterparts.
When it comes to onsite production, the only real restraint is gravity. Everything else can be calculated for and adjusted to meet the needs of the printer.
Examples of 3D concrete Printing
Housing
This 3D printed house in Antwerp, Belgium was the first 3D printed building which was approved for residency. The two story build is 160 sq metres, the entire print took only took 36 days including all fittings, floors and ceilings. The ground floor took 28 days to print and the top floor only 8 days. This includes load bearing and non-load bearing walls.
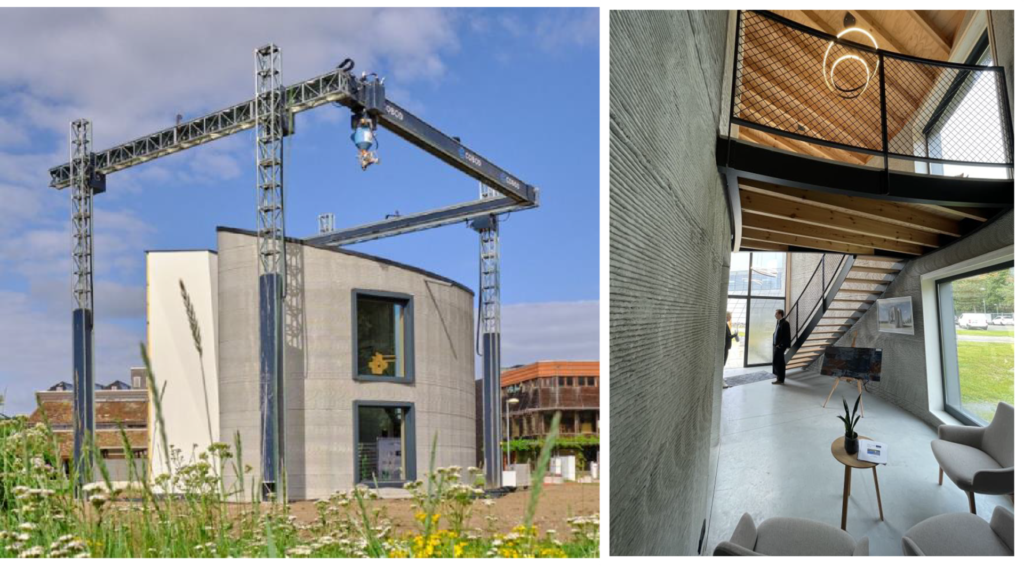
Another example of 3D printed housing is this 3 story build in Wallenhousen Germany. This entire build was completed in 21 days from machine setup through to full completion. The new owners of this house moved in in Q2 of 2021. The three stories each took 7 days to complete.
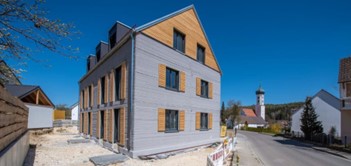
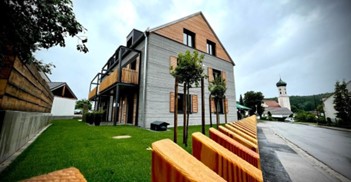
3D Printed Schools
This build in Lilongwe, Malawi was the first 3DCP school in the world and was erected in only 18 hours. This 56 sq metre build has the potential to revolutionise the way we build social and commercial buildings.
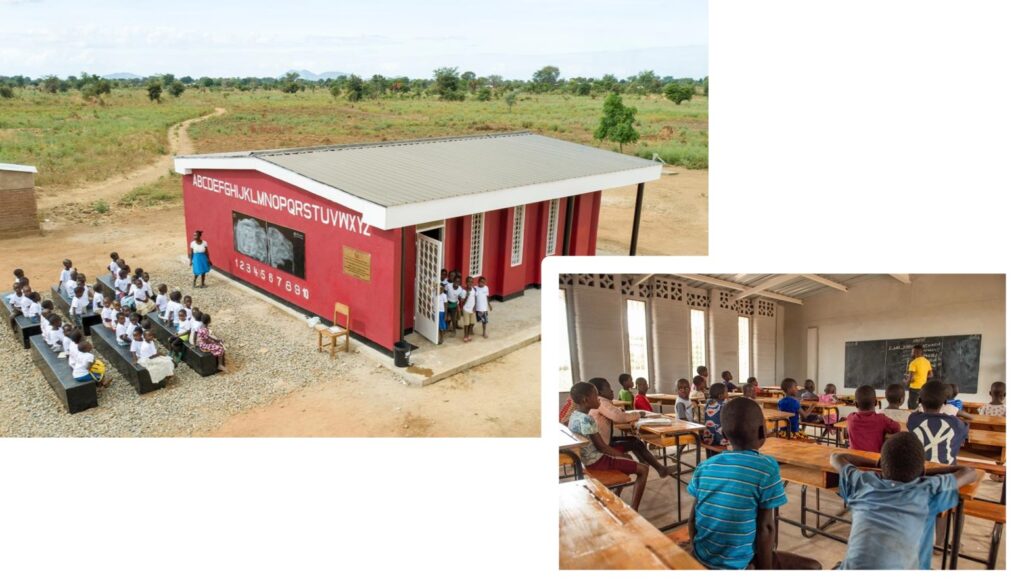
To learn more about how concrete 3D printing is changing the way we build, read more about the Future Cast & HTL printer here.